SOURCE
Stuttgart Operated University Research CubeSat for Evaluation and Education
SOURCE (Stuttgart Operated University Research CubeSat for Evaluation and Education) is a nanosatellite with dimensions of 10 x 10 x 36 cm that complies with the 3U+ CubeSat standard. It is being developed in a cooperation between KSat e.V. and the Institute of Space Systems (IRS) at the University of Stuttgart. As a student CubeSat, it is developed and operated exclusively by students under the supervision of the IRS. As part of the “CubeSat Technology Internship” module, many students have the opportunity to gain practical experience over the course of a semester and earn credit points for their work on the project. In addition to supervising the project, the IRS offers numerous opportunities to test and develop components. In addition, SOURCE is funded by ESA’s Fly Your Satellite! programme, which enables students to learn how to develop, test and document according to the standards of the European Cooperation for Space Standardization (ECSS).
SOURCE carries several scientific payloads, which are divided into two mission phases. Two cameras were integrated on SOURCE for the first phase. The MeSHCam (Meteor, Star and Horizon Tracking Camera) is used for meteor observation as well as star and horizon tracking for position determination. In addition, the smaller PRIma (PR imager) color camera is on board, which is used for PR images of the Earth. The second mission phase begins at 200km and examines the atmosphere during SOURCE’s re-entry. This includes FIPEX sensors on the front and rear sides, which measure the atomic oxygen concentration in orbit. In addition, heat flow, temperature and pressure sensors distributed around the satellite will collect data on the CubeSat’s environment.
Our Payloads
Mission Phase 1 - Orbit at 500km Altitude
Startracking
SOURCE’s star tracking system is an innovative method for determining the position of stars using an inexpensive, commercially available camera. First, the so-called Meteor, Star and Horizon Tracking Camera (MeSHCam) photographs the starry sky in space. The payload onboard computer then compares the images with known star patterns in order to precisely determine the orientation of SOURCE. This use of Commercial-Off-The-Shelf (COTS) components for star tracking is a pioneering technology demonstration as it shows that low-cost, off-the-shelf components can meet the stringent requirements of spaceflight without the need for specialized and more expensive equipment.
Meteor-Detection
The meteor detection payload on board SOURCE aims to observe meteors in the upper atmosphere. The data can expand our understanding of the origin of the solar system. The MeSHCam is capable of detecting even faint meteors, as the light from meteors in orbit is not absorbed by the atmosphere. The use of a commercial camera for these observations also demonstrates the potential for CubeSats to use low-cost optical systems for scientific studies in space. To distinguish between meteors and the background, the payload onboard computer runs the SpaceMEDAL detection algorithm, which is being developed by students at the University of Stuttgart.
PR Images
The PR Imager (PRIma) camera is also a low-cost, commercial camera without special qualifications for use in space. The camera is mounted at a slight angle on the front of the satellite. In contrast to the MeSHCam, the PRIma camera has a high-resolution color sensor. The small camera, measuring 3.5 cm x 2.5 cm, can therefore produce PR photos of the earth. One photo covers a ground area of approximately 450 km x 340 km, which corresponds to around 40% of the area of Germany.
Mission Phase 1 - External Payloads
IRAS – Multifunctional sandwich structure
SOURCE is the test platform for a 3D-printed, multifunctional sandwich structure (MSS) of the German Aerospace Center (DLR) Stuttgart and the Fraunhofer Institute for Manufacturing Engineering and Automation (IPA) as part of the Integrated Digital Reserach Platform for Affordable Satellites (IRAS) project. The IRAS MSS consists of a honeycomb structure made of carbon fibers. At certain points, the structure contains tungsten, which protects the electrical circuits from radiation. A small loudspeaker is also integrated, which can be used to confirm the integrity of the structure in space.
Thin-film solar cells
Almost every satellite mission requires solar cells to generate electricity. Reducing the weight of the cells would therefore offer major advantages for many missions. The DLR Institute of Space Systems is therefore investigating the performance of thin-film solar cells on SOURCE. In addition to saving mass, these also offer the advantage of being flexible: this means that more solar cells can be accommodated in a small space during the launch before they are deployed in space. On SOURCE, the thin-film solar cells are mounted on the top, right next to the satellite’s main solar cells.
IRAS SmartHeater
In cooperation with Airbus Defense & Space through the IRAS project, a SmartHeater is integrated on SOURCE. This component automatically heats up to a fixed temperature when voltage is applied.This eliminates the need for temperature sensors or a control algorithm on the satellite.This makes the thermal system much more robust against software errors.In addition, unlike conventional heating elements, the SmartHeater contains a continuous matrix. Even punctual damage therefore does not hinder the operation of the SmartHeater.
Mission Phase 2 - Re-entry from 200km Altitude
Re-entry
SOURCE’s Re-Entry Measurement Payload is designed to investigate the conditions during the CubeSat’s re-entry into the Earth’s atmosphere. This includes pressure, temperature and heat flow measurements. The sensor data can be used to develop better material models for satellites, making it easier to predict re-entries. In addition, future satellites can be constructed according to the “design for demise” principle. This can prevent dangerous fragments from falling to earth instead of burning up completely in the atmosphere.
Atomic Oxygen
The sensors of the Flux Phi Probe Experiment (FIPEX) are another component of the re-entry sensor system. One sensor is attached to the front and one to the back of SOURCE. The sensors are heated to 800°C in order to determine the content of atomic oxygen in the environment. Atomic oxygen is very reactive and therefore leads to severe corrosion on all exposed surfaces. This affects solar cells in particular, causing the generated power to drop continuously over the duration of the mission. Therefore, accurate models for predicting the concentration in the orbit of a satellite are very important. SOURCE can complement these models well.
SOURCE Subsystems
Project Lead
The student project management team keeps track of everything. Whether it’s the schedule, team events, financing or public relations: this is where everything comes together. The project management is supported by staff from the Institute of Space Systems.
System Engineers
Mechanical, electrical and data interfaces between subsystems are coordinated by the system engineers. This also includes the management of mass and power budgets. The system engineers also plan all the necessary tests. In addition, all test documentation is compared with the internal test standard in order to promote high quality.
We are looking for you!
Has SOURCE piqued your interest? We are always on the lookout for new members!
No matter whether you are just starting out in your first semester or are already a space expert and no matter what you are studying: we can find an exciting position for everyone in our team.
If you already know what you want to do, get in touch with us!
Participation in SOURCE is voluntary or possible as part of the subject-related SQ Praktikum CubeSat-Technik if you are studying at the University of Stuttgart. In addition, SQ participation is also possible as part of our SOURCE-2 and ATHENE projects. 3 ECTS will be credited for participation.
Fly Your Satellite!
Curious?
The Fly Your Satellite! program always offers the opportunity to support student teams in the development of their satellite.
It’s worth visiting the ESA website for the latest updates!
Timeline
Start of the SOURCE project
Following the success of the Flying Laptop (FLP), the small satellite association KSat e.V. and the Institute of Space Systems IRS at the University of Stuttgart decide to build a CubeSat.
PRR (Preliminary Requirement Review) and start of phase B
At the University of Stuttgart, the students of the SOURCE team present the exact boundary conditions of the mission. This concludes phase A, the mission analysis, and phase B, the definition phase, begins.
PDR (Preliminary Design Review) and start of phase C
More than 70 reviewers, including members of Tesat-Spacecom, Thales Alenia Space, Airbus, DLR Bremen and friendly space groups, assessed the presented preliminary design of SOURCE. The reviewers agreed that SOURCE can proceed to Phase C, in which the final design is developed through iterative testing of units.
Announcement Fly Your Satellite
The European Space Agency (ESA) is launching a call for proposals for the third round of the "Fly Your Satellite!" programme, which aims to support university students in the development and launch of CubeSats.
Selection of SOURCE for Fly Your Satellite
The SOURCE team participates in the selection workshop at the ESTEC research center in the Netherlands and is selected as one of four projects to participate in the "Fly Your Satellite! 3" program.
Completion of the CDR (Critical Design Review)
The review board of the "Fly Your Satellite!" program confirms the quality and completeness of the SOURCE design, enabling the transition to the integration phase.
Start of Phase D – Integration and Testing Phase
SOURCE is entering Phase D, where the satellite hardware is built, tested and assembled into a complete system.
Construction of the structural model and system-wide shaker tests
From January to March, SOURCE will be fully integrated for the first time. The goal is to qualify all units in a shaker test of the entire system. After the test campaign, SOURCE will be fully qualified to withstand the stresses of launch in a rocket.
Carrying out the MRR (Manufacturing Readiness Review)
The "Fly Your Satellite!" program team checks the qualification of all components very carefully. After the review, it is clear: The SOURCE team can start producing the flight hardware.
Planned launch of the SOURCE satellite
The SOURCE satellite is scheduled to launch in early 2026, although the exact date will depend on launch vehicle availability and other factors.
More about this Topic
Gallery
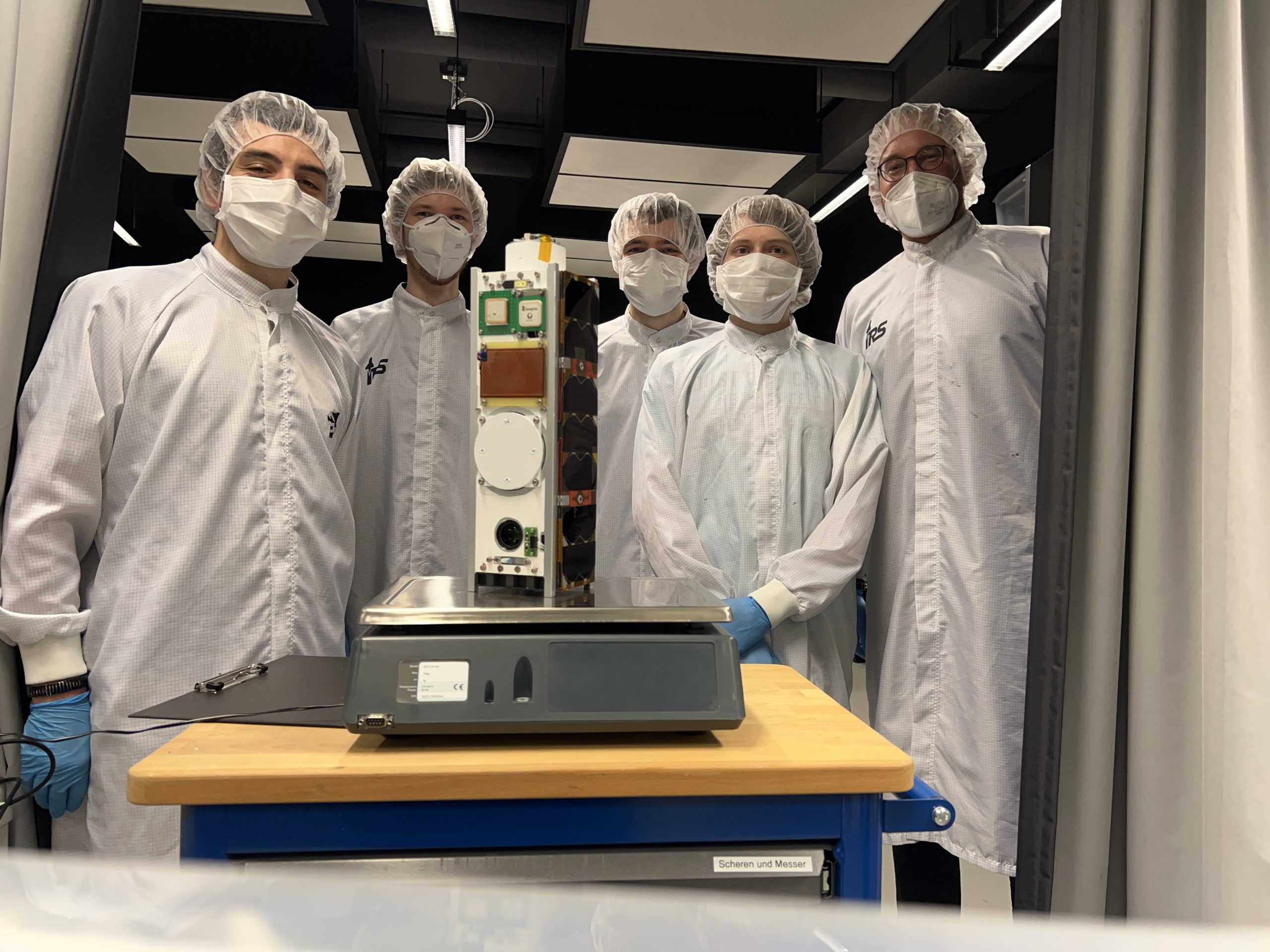
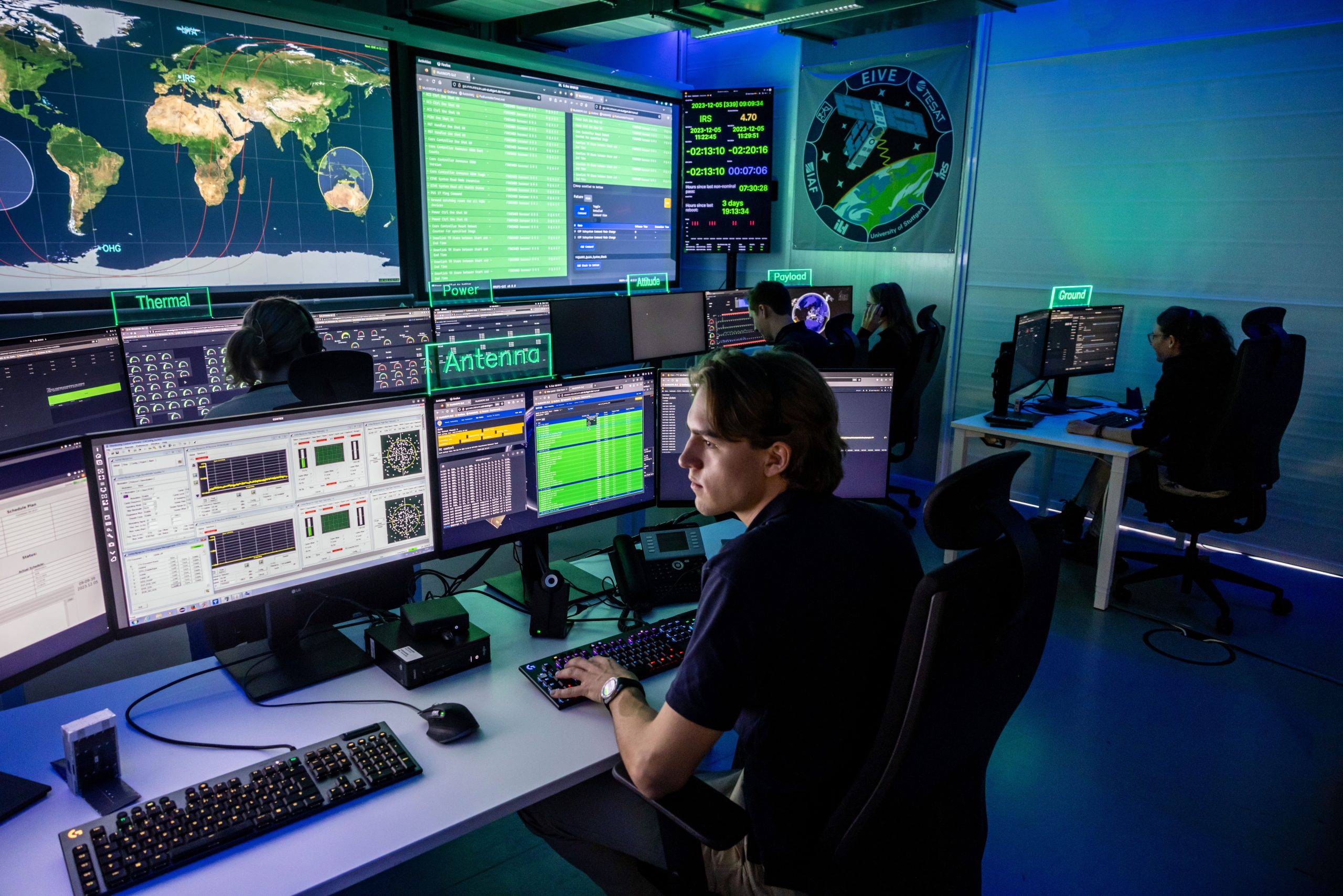
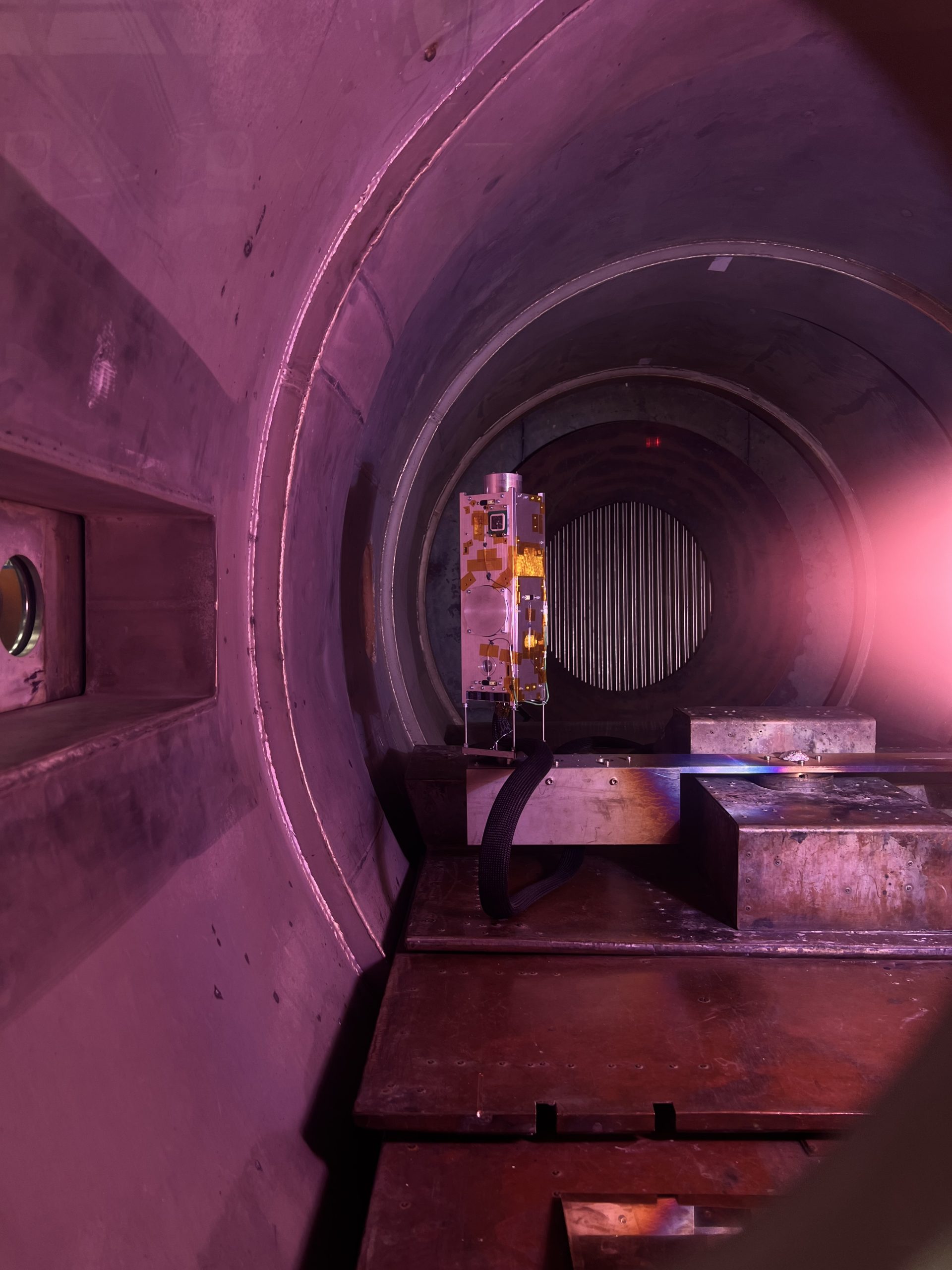

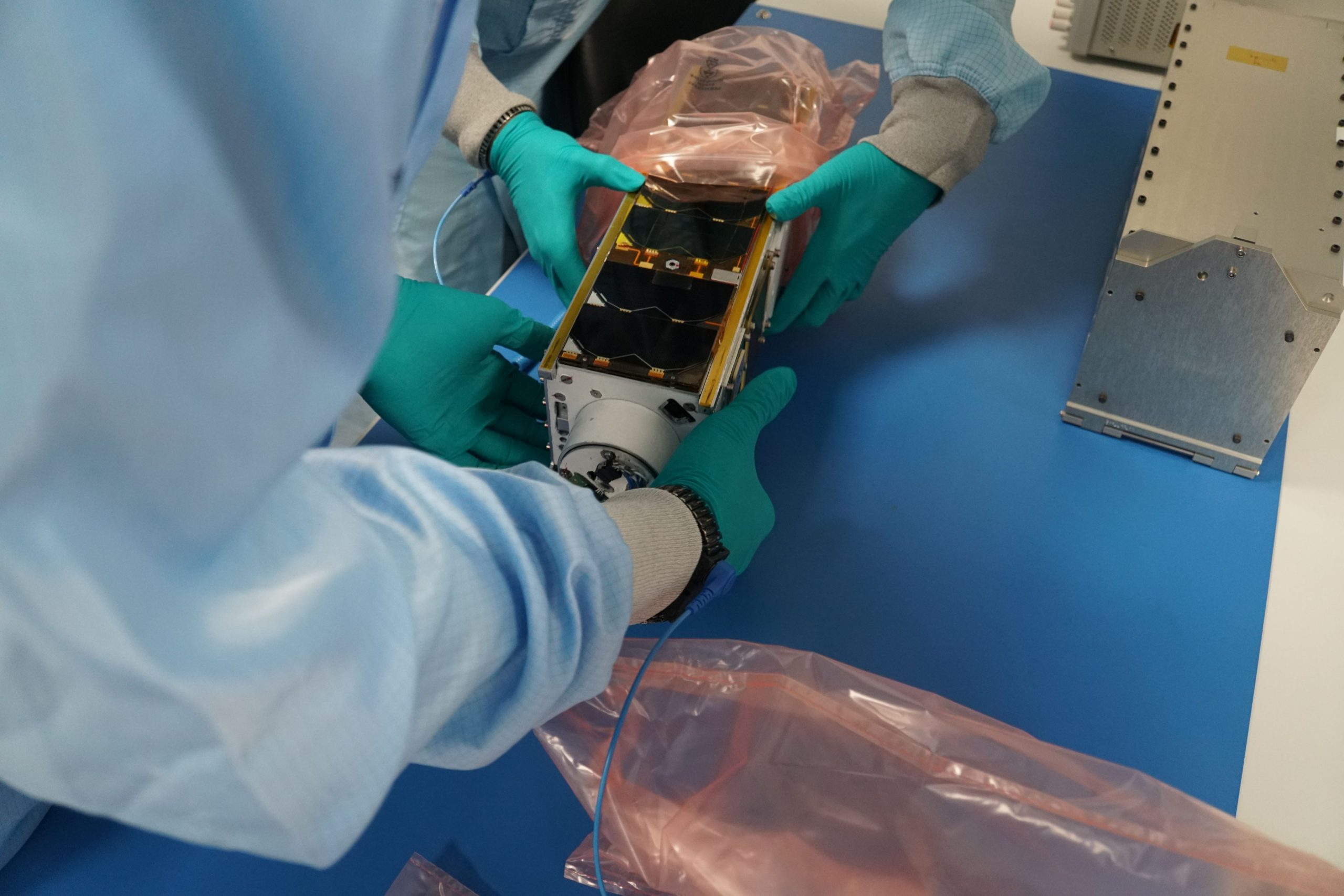
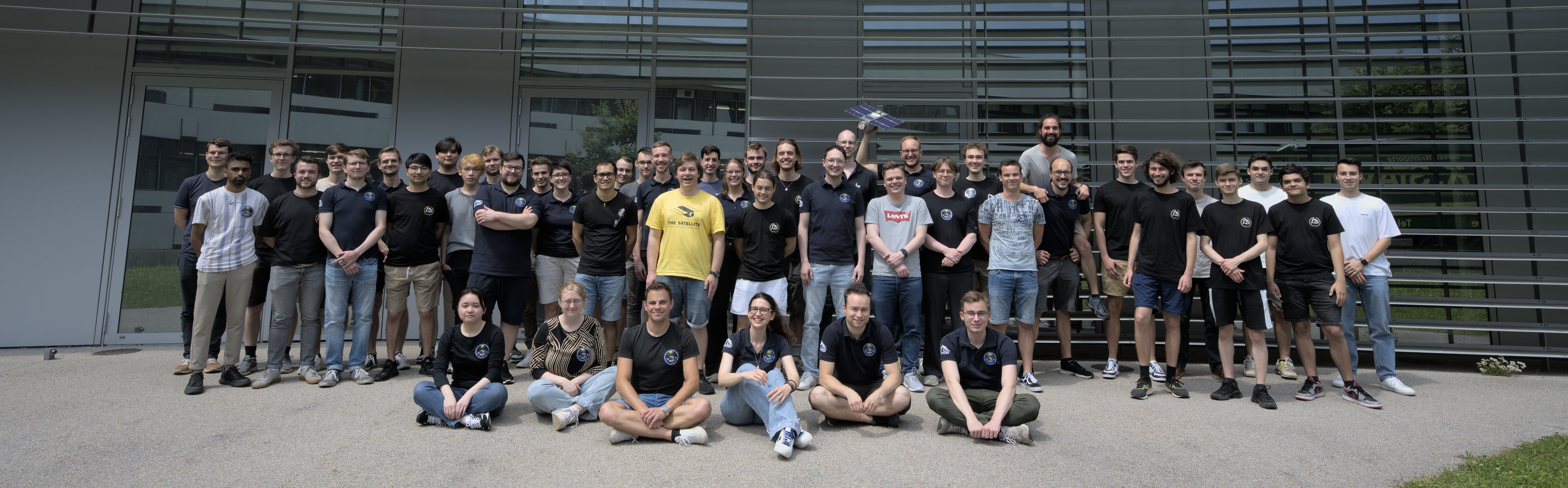
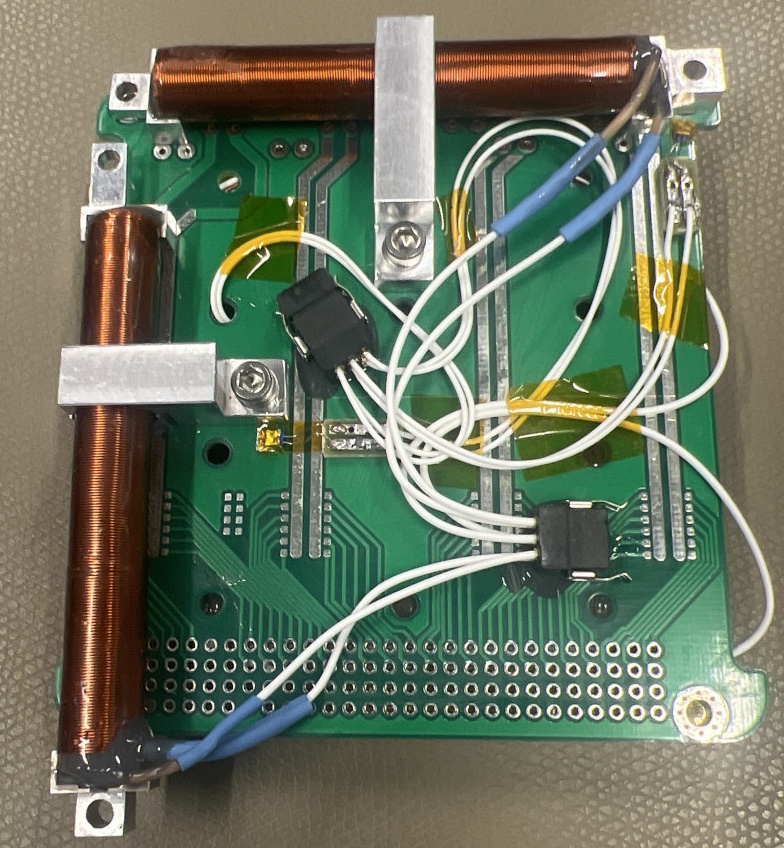
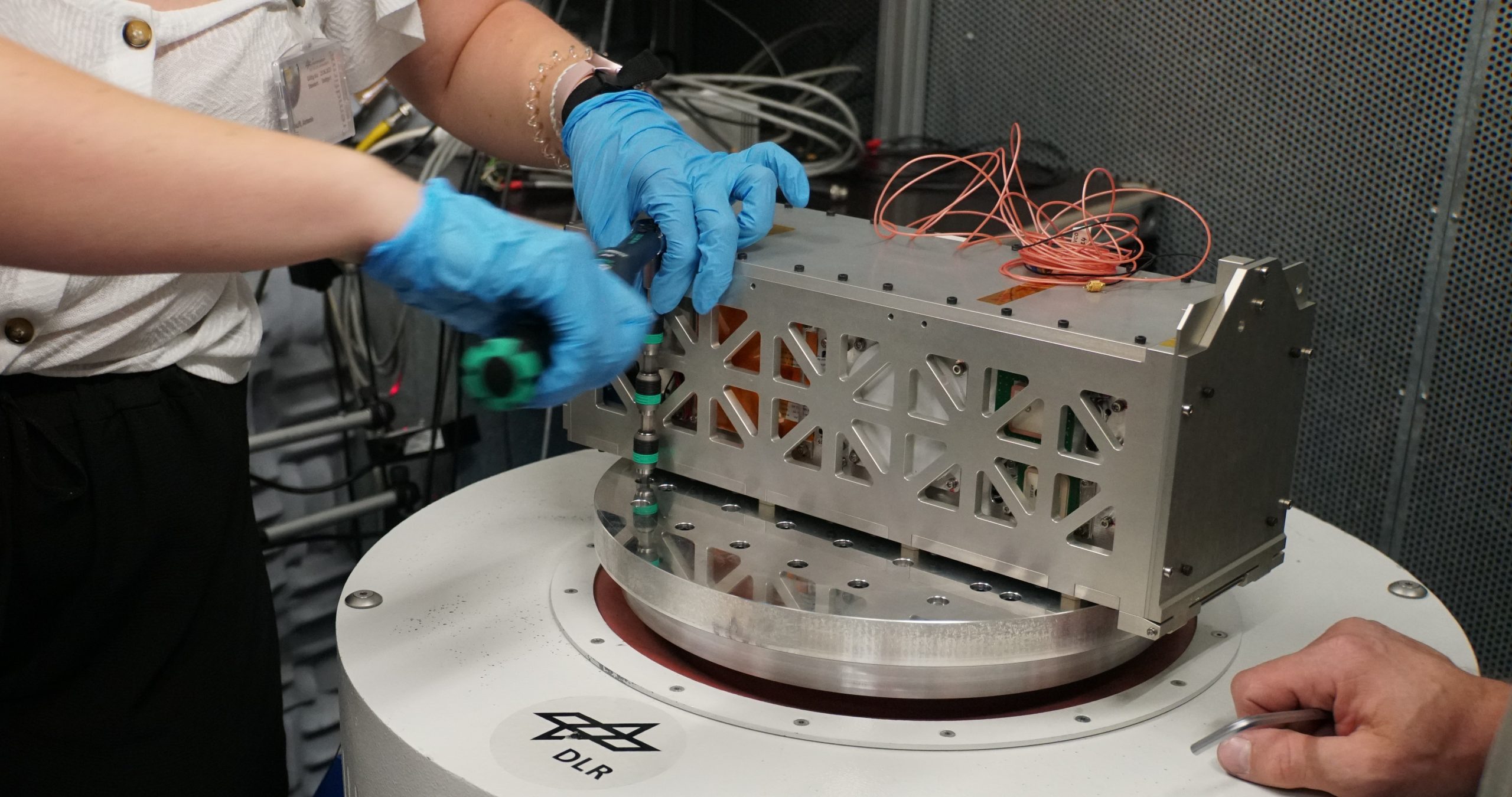
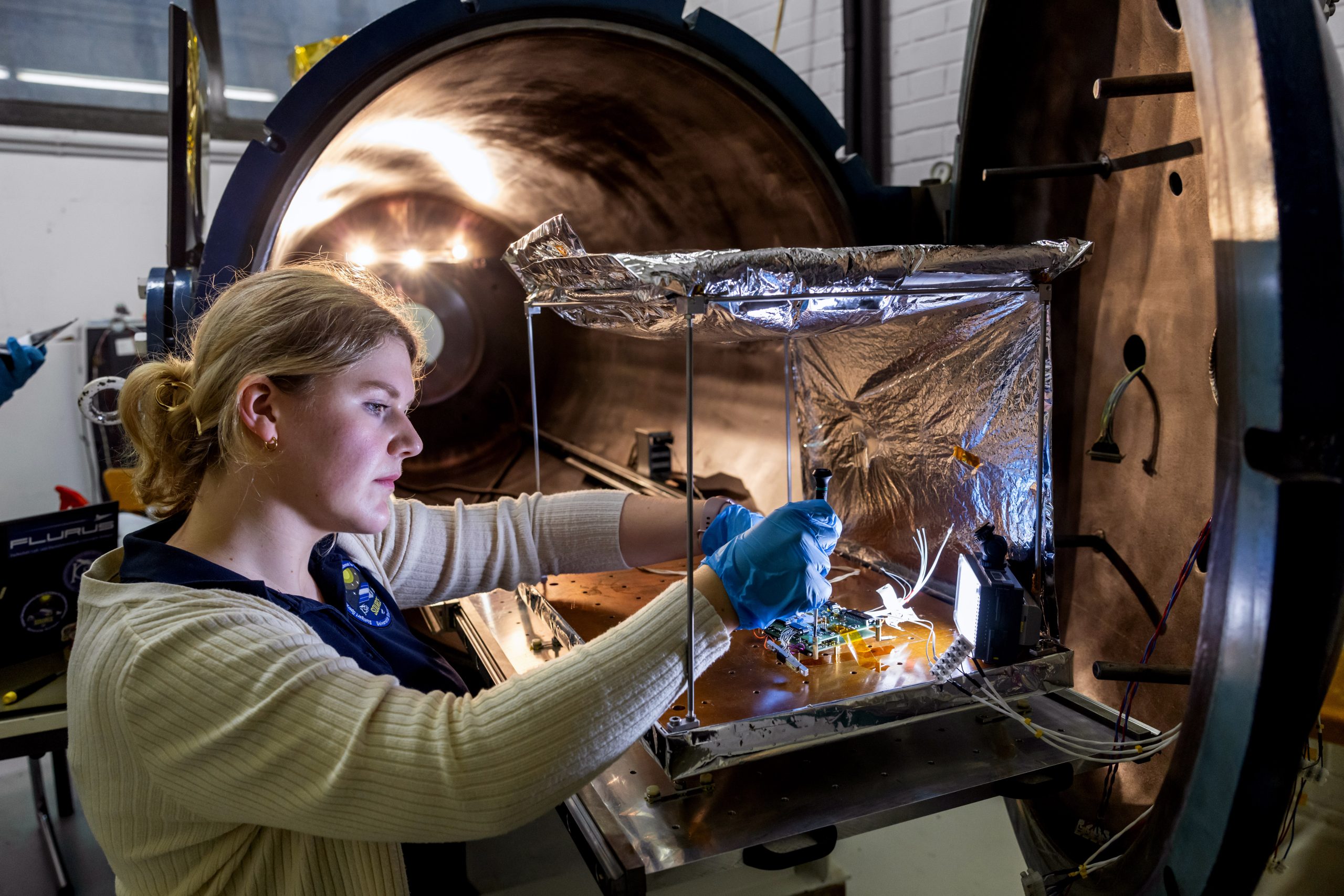
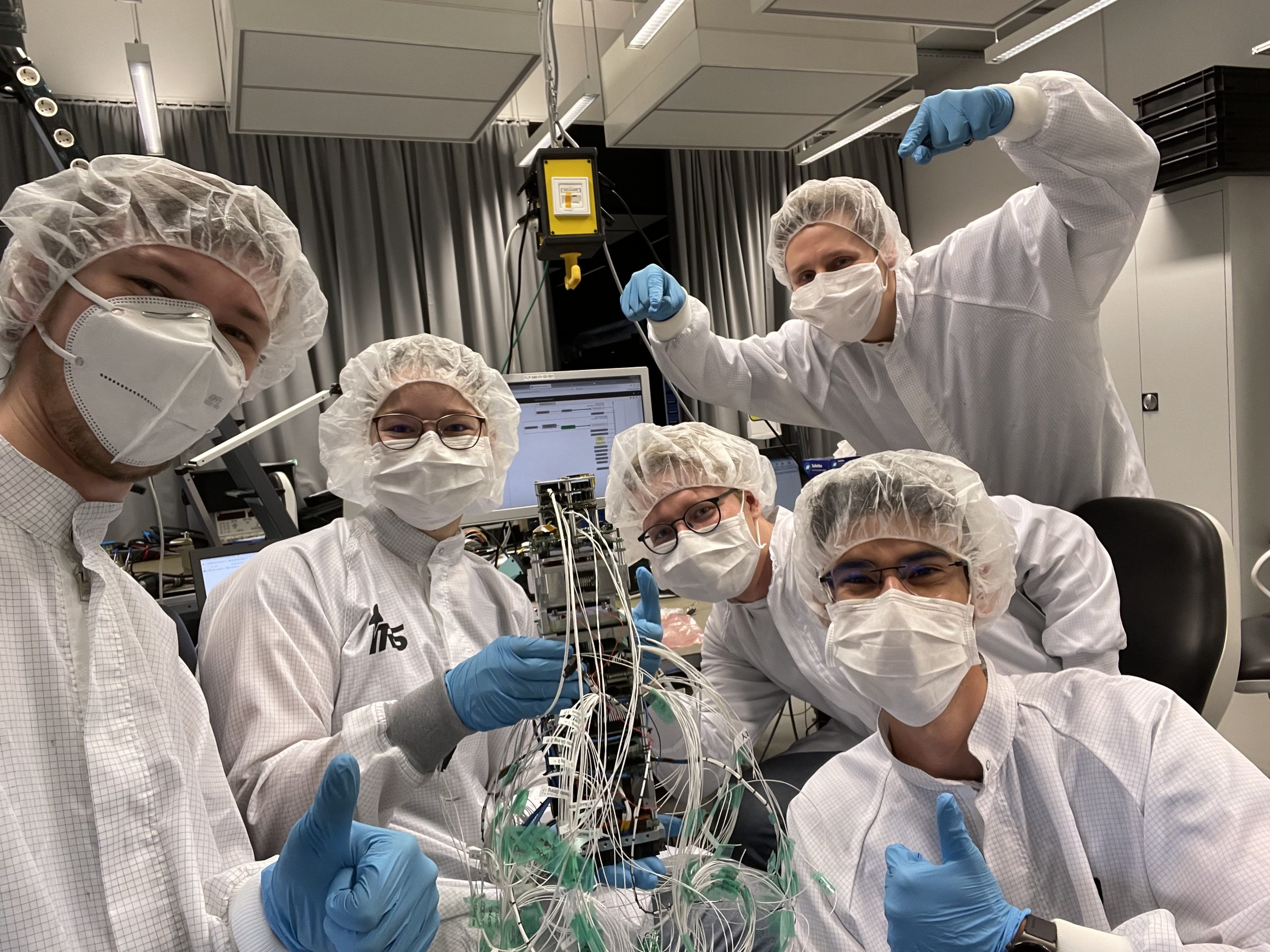
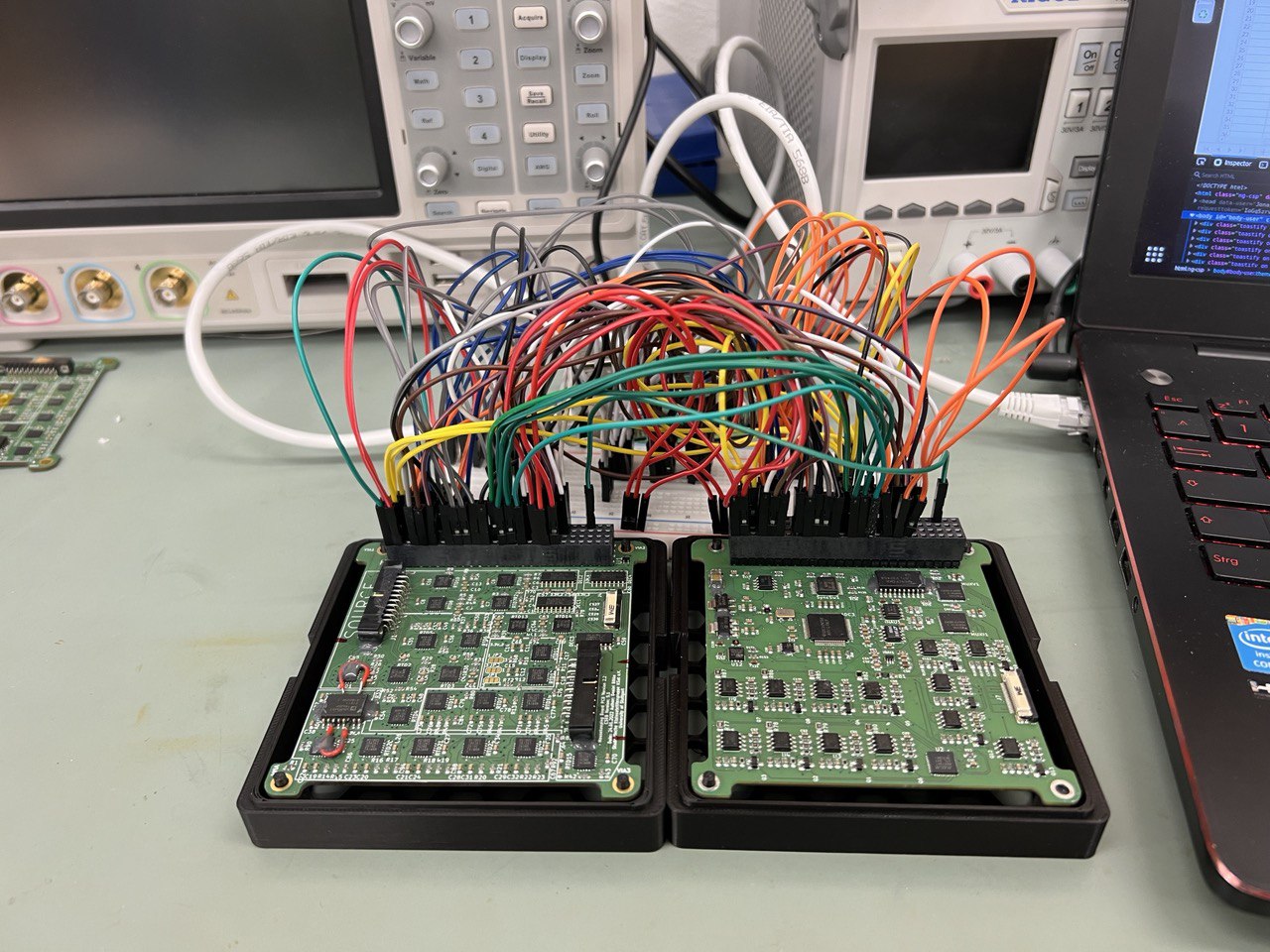
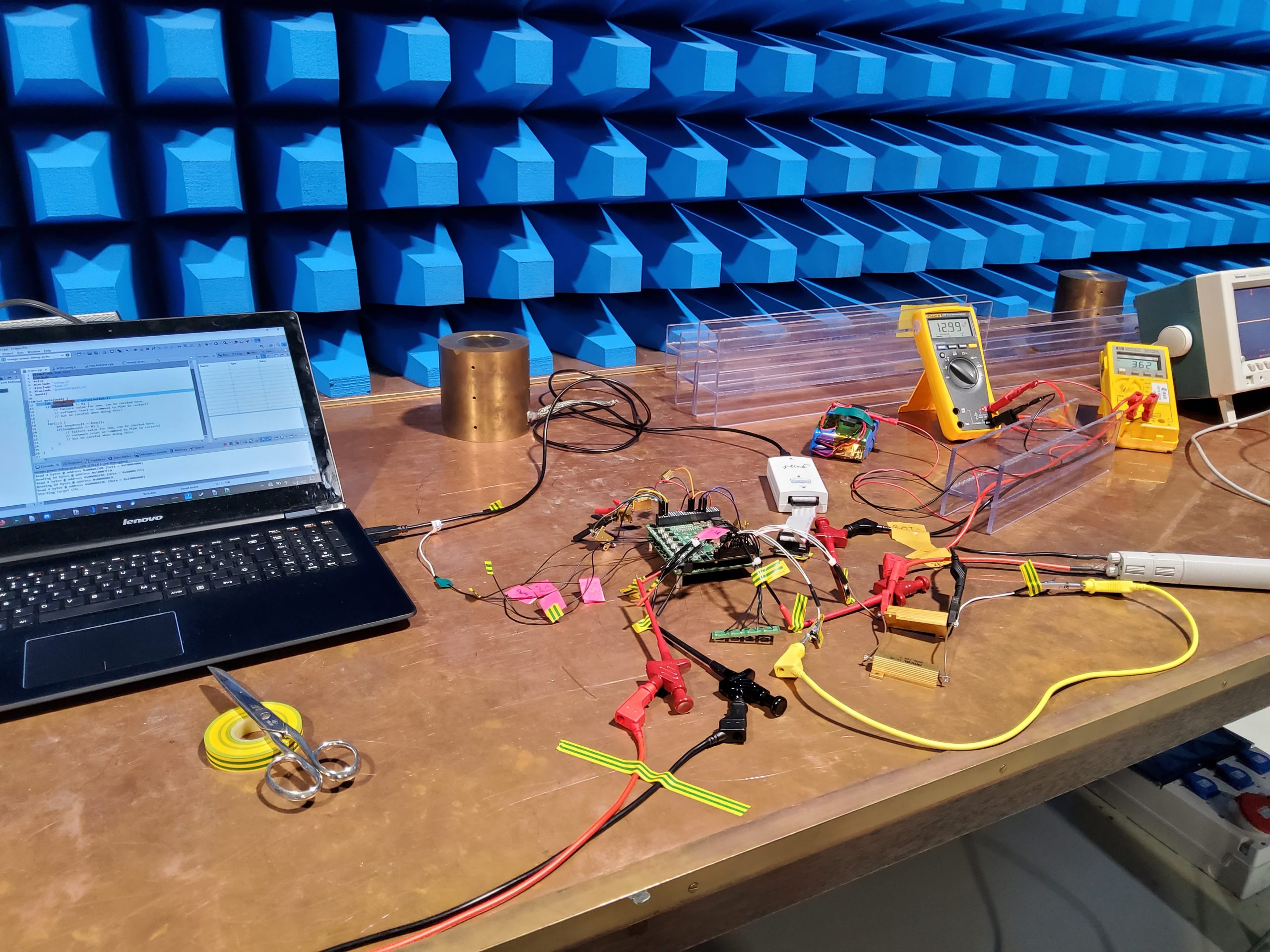
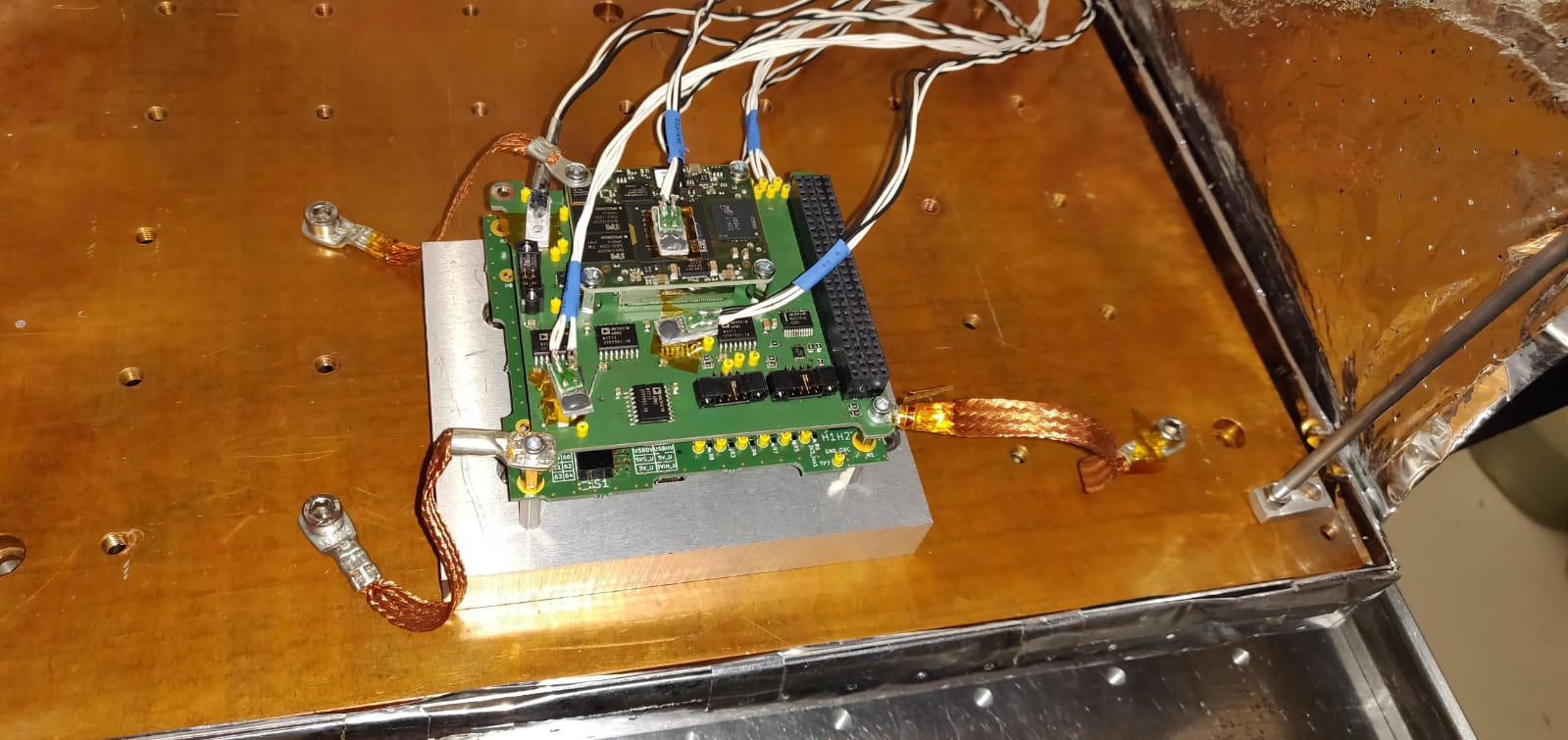